Steel is an alloy of iron and carbon, with carbon content upto a maximum of 1.5%. Most of the steel produced now-a-days is plain carbon steel or simply carbon steel. It is divided into the following types depending upon the carbon content:
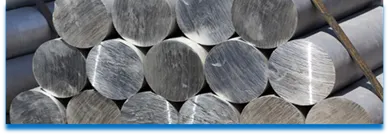
1. Dead mild steel — upto 0.15% Carbon
2. Low carbon or mild steel — 0.15% to 0.45% Carbon
3. Medium carbon steel — 0.45% to 0.8% Carbon
4. High carbon steel — 0.8% to 1.5% Carbon
Our cities stand on the basic foundation of steel, without which they would instantly collapse. How is this outstanding alloy made? Here we discusses the various methods normally employed during the steel manufacturing process.
· - Steel is basically up of an alloy of carbon and iron, where the presence of carbon may vary from 0.25% to 1.5% and hence steel is primarily classified as low carbon steel (around 0.25% carbon), medium carbon steel (between 0.25% to 0.75% carbon) and high carbon steel (0.75% to 1.5% carbon).
· Cementation Process
· Crucible Process
· Bessemer Process
· Open-hearth Process
· Electric Process
· Duplex process
· L-D Process
Let’s look at these one by one.
Cementation Process:
In this process wrought iron bars are introduced in a furnace in between powdered charcoal layers and are subjected to a very high temperature – about 7000 Celsius for about a week to fortnight depending upon the required quality of the steel. The conditions slowly diffuse carbon into iron and cause the carbon to become dissolved in the iron, raising the carbon percentage. Steel obtained from this process is called “blister steel" due to the blister-like marks formed on the surface due to the evolved gases during the manufacturing process. The carbon amount here is usually around 0.75% to 1.5%.
Crucible Process:
The process involves heating of either blister steel fragments or short lengths of wrought iron bars mixed with charcoal inside fire clay crucibles. The resulting molten steel is allowed to run through iron moulds. Such steel is called “cast iron." Cast steel is extremely hard and perfectly homogenous. These are specifically used for making cutting tools and the finest cutlery items.
Bessemer Process:
In this process pig iron is melted in a cupola and poured into Bessemer converter which is pear shaped and has a steel shell lined with refractory material. It’s pivoted on trunnions so as to facilitate tilting, pouring or charging.
Once the above converter is charged with molten pig iron, a strong thrust of air is blasted across the molten mass for about 20 minutes through nozzles provided at the bottom of the vessel. The process oxidizes all traces of the carbon and silicon present, leaving the converter with pure iron.
After this the blasting of air is stopped and the specified amount of ferro-manganese is added to it for the sake of including the recommended content of carbon and manganese to the steel.
The air blasted procedure is again initiated for some time, ensuring perfect mixing of the alloy.
The converter is then tilted so that the molten material can be discharged into the ladles. In the final step the molten alloy is
shifted into rectangular moulds where it’s obtained in the form of solid ingots.

Open Hearth Process:
The specialty of open-hearth furnaces is the extreme heat that can be obtained from them due to their regenerative process. The charge of pig iron, steel scrap, iron ore, and flux are together kept in a shallow container with a flame burning above it. The process is initiated inside reverbaratory gas-fired regenerative furnaces for greater efficiency.
Regenerators are placed below the furnace and positioned in two pairs. The pairs are heated alternately through the passage of hot gases given out from the furnace in their route to the chimney. This heat is retained by the regenerators and is reversed and given back to the furnace. This heat exchange procedure helps the furnace to maintain high temperatures even with less fuels.
Once the furnace is charged with pig iron, pure oxidizing ores like haematite are added to it from time to time, which helps oxidization and the removal of impurities like silicon, carbon, and manganese in the pig iron. Spiegel is also introduced when the carbon content becomes less than 0.1%, and ferro-manganese after the metal is tapped out into the ladle. Ferro-manganese becomes important for restoring malleability and also for carburizing the iron.
Electric Process:
In this process electric arc or electric high frequency furnaces are used. In electric arc furnaces which are more common among the two processes, high voltage electric arc struck between carbon electrodes and the charge becomes the source of a very high temperature. The charge is collected directly from an open hearth furnace, the intense arc heat keeps the charge in its molten state, and the impurities are removed in the form of slag.
The high frequency furnace is based on the principle that when high frequency alternating current is applied to steel, eddy currents starts flowing in them. If this induction is made very strong, it can heat up the steel and melt it.
Electric furnaces are more advantageous compared to the other steel manufacturing processes due to the absence of evolving gases, fumes, etc., which normally become a major problem with fuel operated furnaces.
Duplex process.
The duplex process of steel making is a combination of acidic bessemer process and basic open hearth process. This process is in operation at Tata Iron and Steel works, Jamshedpur (Bihar).
L-D process (Linz-Donawitz process).
It is the latest development in steel making processes and is now adopted at Rourkela steel plant where three converters of 40 tonnes capacity are working.
Note : The bessemer process may be acidic or basic depending upon the lining of furnace. In the acidic bessemer process, the furnace is lined with silica ricks. The slag produced in this process contains large amount of silica. Since phosphorus in a pig iron cannot be removed by this process, therefore acidic bessemer process is unsuitable for producing steel from pig iron containing large quantities of phosphorus.
In basic bessemer process, also known as Thomas process, the furnace is lined with a mixture of tar and burned dolomite. This process is applicable for making steel from pig iron which contains more than 1.5% phosphorus.
Note: The steel contains small amounts of impurities like silicon, sulphur, manganese and phosphorus. The effect of these impurities are as follows:
Silicon in the finished steel usually ranges from 0.05 to 0.30%. It is added in low carbon steels to prevent them from becoming porous. It removes the gases and oxides, prevents blow holes and thereby makes the steel tougher and harder.
Sulphur occurs in steel either as iron sulphide or manganese sulphide. Iron sulphide because of its low melting point produces red shortness whereas manganese sulphide does not effect so much.
Manganese serves as a valuable deoxidising and purifying agent, in steel. When used in ordinary low carbon steels, manganese makes the metal ductile and of good bending qualities. In high speed steels, it is used to tougher the metal and to increase its critical temperature.
Phosphorus makes the steel brittle, It also produces cold shortness in steel. In low carbon steels, it raises the yield point and improves the resistance to atmospheric corrosion. The sum of carbon and phosphorus usually does not exceed 0.25%.
0 Comments